Epoxy Floors for Air Hangers
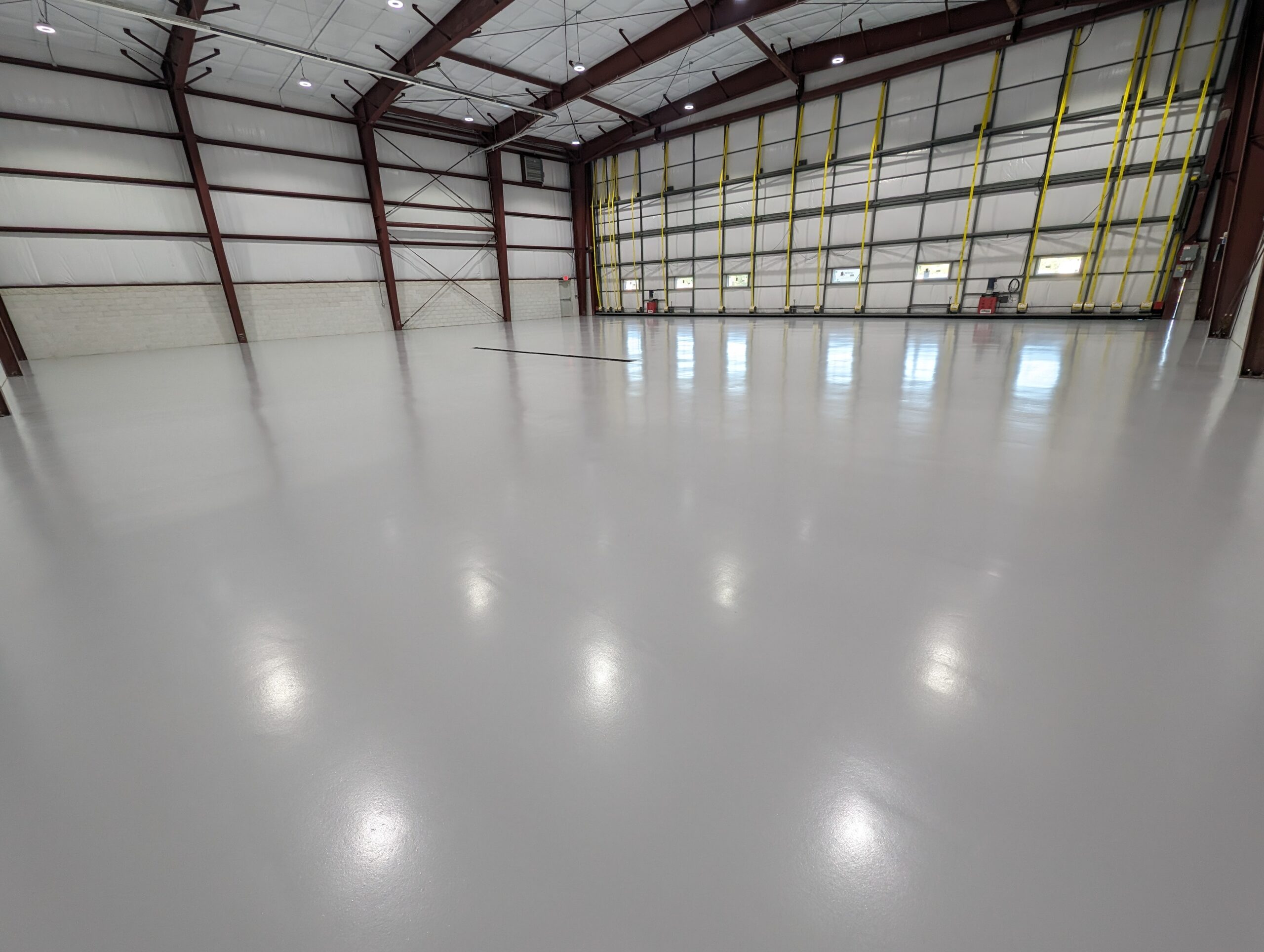
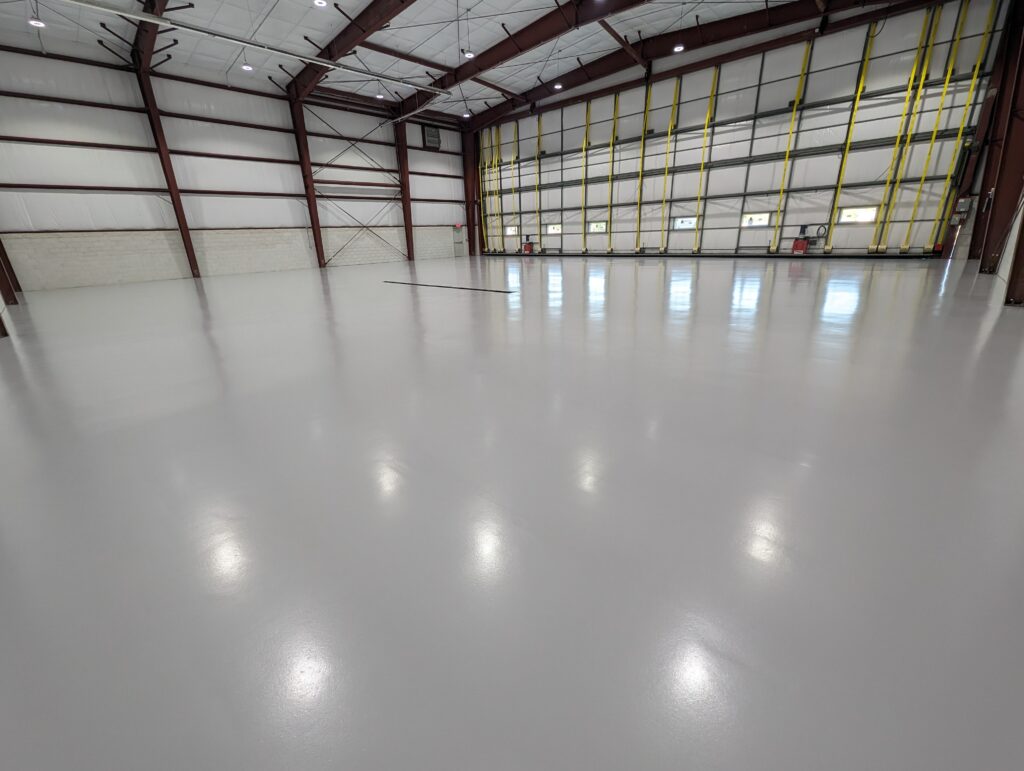
Air hanger floors are subject to many corrosive liquids, heavy equipment, and hard hardware. These materials can deteriorate the concrete floors when exposed over time. Hydraulic fluids or jet fuel won’t deteriorate the concrete in one drip. But with constant exposure, it can saturate the floor, penetrate the capilaries in the slab, and slowly cause the concrete matrix to deteriorate.
Tools and equipment won’t damage the concrete slab in just one moment. But constant tools be dropped, heavy planes and helicoptors, and tires driving over hardware can cause a lot of damage to the cream of the concrete cap over time.
For these reasons, it’s a great idea to introduce an epoxy flooring company to install an epoxy flooring system in your air hanger.
But which system? There’s a variety of systems you can introduce: epoxy, methyl methacrylic, and urethanes. But which one is the best option? Each resinous flooring system has a variety feature and benefits, and knowing the purpose of each hanger will help decide which flooring system to install.
Epoxy and Urethane floor systems
The goal with coating your concrete is to create a high gloss, with zero color distractions. This reason is so mechanics working on planes can easily nuts, bold, tools, and hardware if they are laying on the floor. Additionally, the high gloss allows light reflection to help mechanics see the underside of the plane.
System
- Base Coat: 8mils of 100% solid epoxy
- Intermediate Coat: 16mils of 100 solid epoxy
- Top Coat: 3mils of aliphatic urethane top coat with aluminum oxide powder
The benefit of this system is that the epoxy body coats will help flatten the floor from any imperfections in the concrete. Grinding the concrete will help remove the imperfections. However, there still may be gauges, divots, and other noticeable defects in the slab. If the defect is too large, it will requiring patching.
The aliphatic urethane top coat is wear resistant and strong enough to tolerate impacts from tools and heavy planes. And with the aluminum oxide powder additive, it makes it stronger against wear and impact.
One drawback with this system is that the aliphatic urethanes are not impervious to tires from airplanes. The tires are loaded with plasticizers, which are known to bond to epoxies and urethanes, causing staining, and for the floor coating to strip. Aliphatic urethanes have tested okay against tires, and adding the wear powder improves that resistance. But it can still happen. MMA floors (methyl methacrylate), which we’ll discuss next, will not disbond against hot tires.
MMA Floors Systems (Methyl Methacrylate)
When searching for an extremely hard wearing coating, MMA floors are typically the top performer. They outperform urethanes against hot tires, and they’ll wear longer than epoxies and urethanes.
Another benefits is that they naturally comes with a low sheen finish. This finish helps hide imperfections that may telegraph through the concrete.
Overall, MMA floors outperform other flooring systems. But the biggest drawback is their odor. They have an extremely noxious odor, and installers need to wear respirators when installing. But the odor dissipates quickly, and provides a great floor at the end of the installation.
System:
- Base Coat: MMA primer at 16mils
- Body Coat: MMA at 60mils
- Top Coat: Top coat at 16mils
This is a much thicker floor system compared to the epoxy system itemized above. But this thicker system will wear longer, and impact longer against tools, equipment and hot tires.